Cada vez que se queman los restos de una poda de olivar se pierden dinero y la oportunidad de transformar esa biomasa en un productos de valor añadido. Un equipo de la Universidad de Jaén (UJA) y el Centro Tecnológico Fundación Andaltec (ADN) trabajan en el desarrollo de nuevos procesos de economía circular, para aprovechar esta biomasa y darle una segunda vida como bioplásticos.
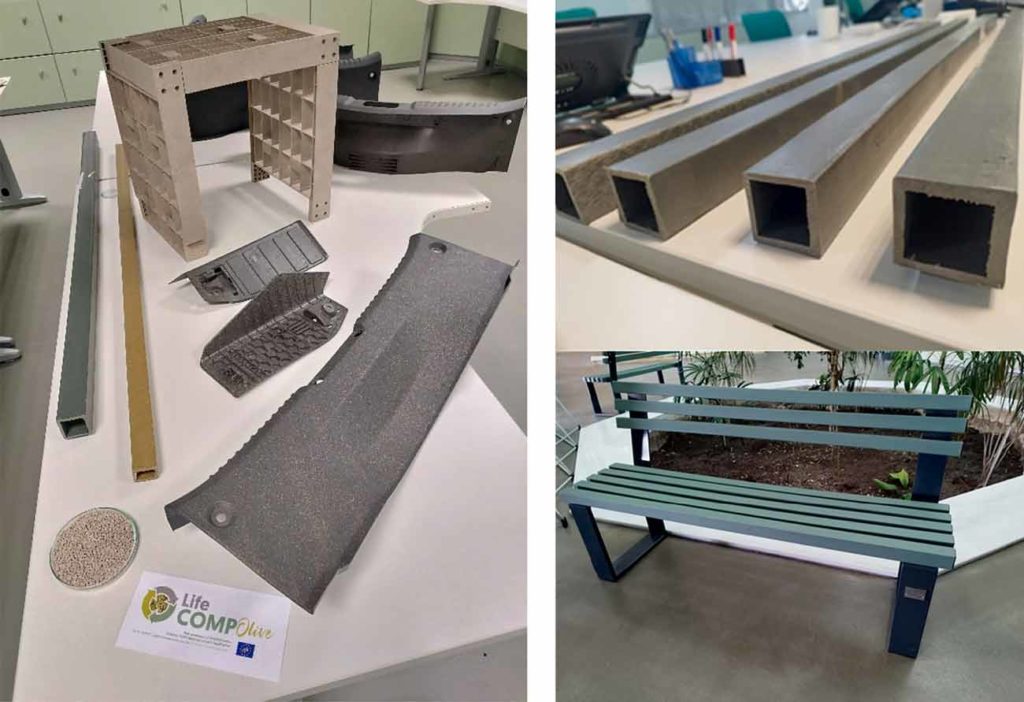
Concretamente, científicos de la UJA y ADN han logrado transformar restos de poda del olivar en plásticos ecológicos de un alto valor, que pueden tener salida en la industria del automóvil, en la fabricación de mobiliario urbano y muebles para el hogar, así como para la elaboración de películas de plástico.
Los trabajos están dirigidos por la investigadora del Departamento de Ingeniería Química, Ambiental y de los Materiales de la UJA, María Dolores La Rubia, y con ellos se han conseguido unos materiales con unas propiedades tan interesantes como las que ofrece el plástico convencional, pero con una huella ambiental mucho menor, prácticamente negativa. Estos bioplásticos generados con restos de poda de olivar son ya una realidad, al menos en laboratorio, y contribuirían a reducir la dependencia del petróleo, además de plantear una salida sostenible a los millones de toneladas de restos de poda de olivar que se generan al año en Andalucía.
Qué bioplásticos se consiguen con restos de poda de olivar
Los plásticos hechos a partir de biomasa vegetal son versátiles y pueden emplearse en sectores de la industria muy diversos. Por ejemplo, en el marco del proyecto Life Compolive, el equipo de María Dolores La Rubia ha conseguido desarrollar biocomposite, un material compuesto, para uso industrial, basado en fibras del olivar.
Tradicionalmente, la industria del plástico ha empleado fibra de vidrio para endurecer el producto final. Sin embargo, se encontraba con que esta fibra es altamente contaminante y no se puede reciclar. Por estos motivos, comenzaron a endurecer el plástico con fibras procedentes de bambú y de otros cultivos similares, dedicados exclusivamente a este fin.
«A nosotros se nos ocurrió sustituir esas fibras de bambú por las resultantes de la poda de olivo. Y probamos con varias concentraciones, hasta llegar a un material compuesto en un 60 por ciento por plástico convencional y en un 40, por restos de poda de olivo», explica María Dolores La Rubia. Esta investigadora llama la atención sobre el ahorro económico y reducción de huella medioambiental que supone emplear este material para fortalecer los plásticos.
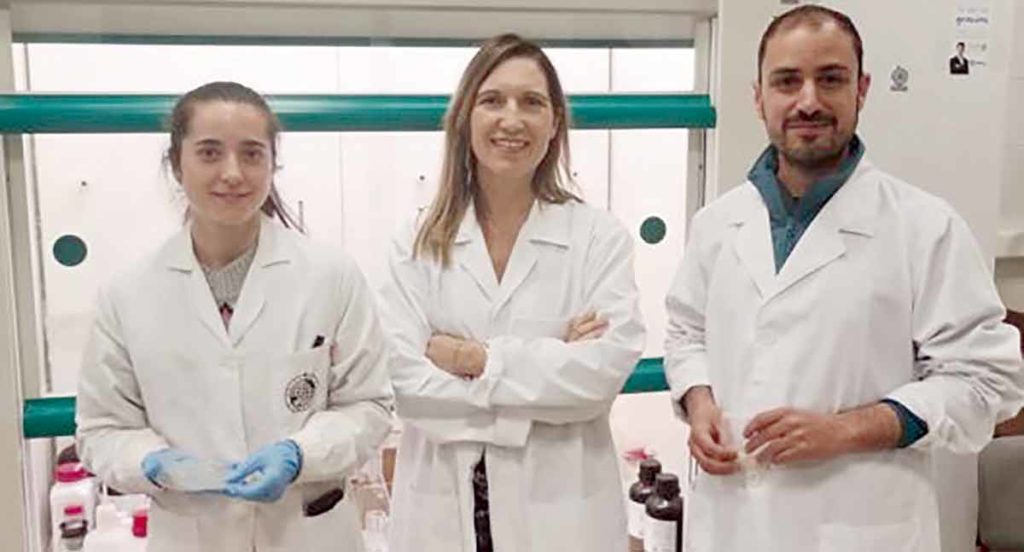
Qué aplicaciones tiene este plástico ecológico
Las aplicaciones del material plástico desarrollado por la UJA son diversas. Se puede emplear el endurecimiento de todo tipo de plásticos, en la fabricación de bancos y otras muchos elementos de plásticos, así como en la fabricación de piezas para coches.
En vista de los resultados y de las propiedades que presentaba este biocomposite, el equipo de la UJA y ADN se puso en contacto con Ford. El fabricante de vehículos, al ver el buen comportamiento del material y que sus propiedades se ajustaban a las exigidas en el sector, decidió incorporarse como un socio más de Life Compolive.
Como resultado de su participación, el grupo de investigación de la UJA y ADN ha desarrollado un biocompuesto plástico especial para la firma estadounidense, que se ha probado en la fabricación del cubremaletero del modelo Focus y del reposapiés de la versión eléctrica del Mondeo. «Ford fabricó en su planta de Valencia unas 300 piezas con este material y comprobó que se ajustan a los parámetros exigidos, por lo que perfectamente podrían emplearse en sus coches», explica la investigadora de la UJA.
Sobre el material desarrollado para Ford no se pueden dar muchos detalles, debido a los contratos de confidencialidad, pero en resumen se trata de un polipropileno reciclado, con un 40 por ciento de fibras vegetales. «El fabricante automovilístico Ford estaría dispuesto a incorporarlo siempre y cuando se le pueda suministrar todo el material que necesitan y eso supone un reto».
La investigadora María Dolores La Rubia confía plenamente en este nuevo material, que también podrían emplear otros fabricantes de la automoción, así como de sectores tan diversos como la construcción, gracias a la versatilidad que presenta este material y las múltiples formulaciones que se pueden obtener con este método. Sin embargo, para que este producto pase del laboratorio a la industria se necesitaría poner en marcha una planta industrial específica en la provincia de Jaén, con la que se dé salida una salida rentable y medioambientalmente muy interesante a una biomasa que actualmente supone un problema para los agricultores.
Esta investigación ha permitido demostrar el potencial de los restos de poda de olivo. Gracias a métodos basados en la economía circular se pueden transformar en productos de valor, que generan riqueza y reducen la contaminación.